Design
Enclosure
Capabilities
Configurations
Charging
|
Proven Innovative Battery Pack Solutions
We offer designs for both primary and secondary chemistries to include, alkaline, NiMH, NiCd, primary lithium, and the latest lithium-ion or lithium-polymer batteries. Our goal is to offer full battery design support to help create a custom pack with optimal size, capacity, voltage, operating temperature range to meet the many varied application demands.
Design & Production Services
At our Engineered Technologies we provide early design guidance, and design services in the following areas:
>>Battery Chemistry Selection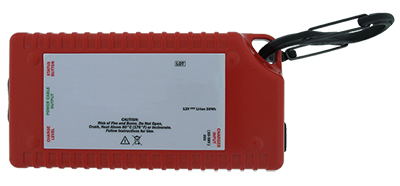
>>Battery Charger Selection/Design
>>Battery Fuel-gauge Suggestions Based On Application
>>Battery Safety-Circuitry Recommendations
>>Battery Construction Suggestions
>>System Architecture Guidance
>>Regulatory Guidance
>>Production Test Equipment
We provide full turn-key services in product development, production of batteries, chargers, and batteries with embedded BMS control.
Portable Power Design
Mechanical Engineering
>>Plastic design with 3-D modeling
>>SLA prototypes, and polyurethane quick-turn molds
>>Production tooling design 
>>Custom Label and Overlays
Electrical Engineering & PCB Design and Layout
>>Custom battery, battery charger, and fuel gauge design
Embedded Firmware Development
>>Custom battery and customer system interface development
Automated Production Test Equipment Design and Development
>>Production test equipment development
Battery Team Experience
We have key team members that have been active within the battery and battery-charger industry since 1996. Our battery team has over twenty-two years of experience in military, medical, industrial, and high-volume consumer industries providing a distinct advantage when developing and qualifying battery designs for use in these industries.
Our experience includes pioneering the development of custom safety circuits and battery chargers for the Li-Sulfur chemistry. We have extensive experience in the development of safety-circuits, fuel gauging, and battery chargers for Li-Ion, and Li-Polymer chemistries. As a result, our team has received numerous patents in their area of work.
Battery Enclosure Design
Some battery packs are installed inside the product, and only require a shrink-wrap enclosure. In other cases, battery packs are mounted externally and may serve a mechanical function, such as a handle or base for the product. At the same time the case must also protect the cells and the electronics from the harsh operating environments of temperature extremes, water ingress, humidity and vibration in which these batteries work.
Injection Molded Plastic
Enclosures made from injection molded plastics are most commonly used for battery packs. For these enclosed pack designs, two or more plastic parts are molded and then assembled with the pack and accompanied circuitry. They can be sealed using glue, mechanical fasteners (Screws) or ultrasonic welding. The product cost can be reduced by using insert moldings in which the interconnection strips and the terminals are molded into the plastic parts to eliminate both materials and assembly costs.
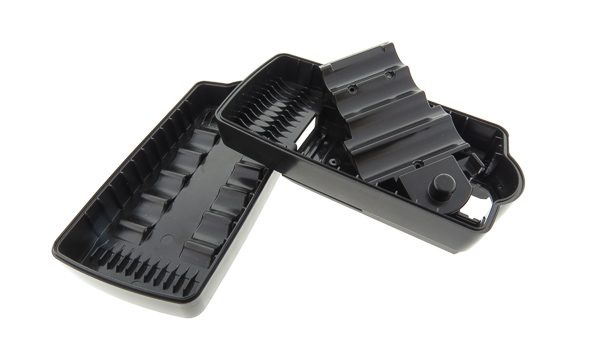
In some designs, the battery pack can form part of the outer case of the end product and usually requires a mechanical latch to hold the battery in place. This latch as well as the terminals must interface with plastic parts from the device itself so high precision and tight tolerances are essential.
Shrink Wrap or Vacuum Formed Plastic
The simplest and least expensive packaging for small batteries is shrink wrap or vacuum formed plastic. These solutions are only possible if the battery is intended to be completely enclosed by the finished product. In other cases, battery packs are mounted externally and may serve a mechanical function, such as a handle or base for the product. Our extensive experience in designing battery enclosures of all types allow us to enhance the functional design of the product while assuring that the battery passes any shock, vibration and environmental testing required for your application.
Other Considerations
Thermal effects need to be taken into account and, tolerances must allow for potential swelling of the cells. Some Lithium pouch cells may swell as much as 10% or more over the lifetime of the cell. For this reason, enclosures may be designed with vent holes to dissipate generated heat or exhaust vented gases from cells. Multiple vent holes may be used to increase airflow in and out of the pack.
Intrinsically Safe Batteries
Intrinsically safe batteries will not initiate and explosion should the electronic device malfunction while operating in areas that contain explosive gases or high dust concentration. For these applications, specific materials are selected for battery pack enclosure and many times potting material is used in the battery pack enclosure to eliminate any air gaps.
Our Plastic Capabilities Include
>>Over Molding
>>Insert and Multi-shot Injection Molding
>>Designing
>>Assembly
>>Heat Staking
>>Hot Stamping
>>Pad Printing
>>Ultrasonic Welding
>>Bar Coding
Various Plastic Materials Include
>>Nylon
>>ABS
>>PP
>>PE
>>PPO
>>Polyester
>>PC and Acrylic
MIER TECH-WISE works with our customers do design and build custom battery packs to exceed their requirements. Our engineering team will help the design team select the best cell type and size for each application along with all of the other mechanical and electrical parameters needed to produce a quality battery product.
Our Battery Capabilities Include:
•Primary Batteries (Non-Rechargeable)
•Rechargeable Batteries (Secondary) ?NiMH, NiCD and Lithium Cells
•Lead Acid Batteries
•Custom Battery Packs ?Design Capabilities (all cell chemistries available in battery packs)
•Smart Packs – Can include integrated fuel gauges, integrated circuits, or communication protocol
•Cell Balancing and Matching
•Cable/Connector Assembly and Custom Terminations
•Thermostats, fuses and protection circuitry
•Custom Enclosures (Plastic or metal)
•Potting and Shrink Wrapping
•DOT, IATA and UL testing and approval
•Assembly drawings provided prior to manufacturing
•Supply Chain Management
•Flexible inventory management programs available (Kanban, blanket orders, consignment)
•All manufacturing facilities are ISO9001:2008 and ISO14000 certified
Our Product Inventory Stocking Programs Include
Kanban Programs
At our facility, we can manufacture and store inventories that can be available on a Just In Time (JIT) basis. We can accept releases via phone or email.
Blanket Orders
Our partner can manufacture and inventory your PCBs at our facility to fulfill your manufacturing scheduling requirements.
Consignment Stock
Our factory can manufacture PCBs on a consignment basis. Inventory may be stocked at either your facility or at our warehouse.
Basic Battery Charging Methods
Constant Voltage
A constant voltage charger is basically a DC power supply which in its simplest form may consist of a step down transformer from the mains with a rectifier to provide the DC voltage to charge the battery. Such simple designs are often found in cheap car battery chargers. The lead-acid cells used for cars and backup power systems typically use constant voltage chargers. In addition, lithium-ion cells often use constant voltage systems, although these usually are more complex with added circuitry to protect both the batteries and the user safety.
Constant Current
Constant current chargers vary the voltage they apply to the battery to maintain a constant current flow, switching off when the voltage reaches the level of a full charge. This design is usually used for nickel-cadmium and nickel-metal hydride cells or batteries.
Taper Current
This is charging from a crude unregulated constant voltage source. It is not a controlled charge as in V Taper above. The current diminishes as the cell voltage (back emf) builds up. There is a serious danger of damaging the cells through overcharging. To avoid this the charging rate and duration should be limited. Suitable for SLA batteries only.
Pulsed Charge
Pulsed chargers feed the charge current to the battery in pulses. The charging rate (based on the average current) can be precisely controlled by varying the width of the pulses, typically about one second. During the charging process, short rest periods of 20 to 30 milliseconds, between pulses allow the chemical actions in the battery to stabilize by equalizing the reaction throughout the bulk of the electrode before recommencing the charge. This enables the chemical reaction to keep pace with the rate of inputting the electrical energy. It is also claimed that this method can reduce unwanted chemical reactions at the electrode surface such as gas formation, crystal growth and passivation. If required, it is also possible to sample the open circuit voltage of the battery during the rest period.
Burp Charging
Also called Reflex or Negative Pulse Charging Used in conjunction with pulse charging, it applies a very short discharge pulse, typically 2 to 3 times the charging current for 5 milliseconds, during the charging rest period to depolarize the cell. These pulses dislodge any gas bubbles which have built up on the electrodes during fast charging, speeding up the stabilization process and hence the overall charging process. The release and diffusion of the gas bubbles is known as "burping". Controversial claims have been made for the improvements in both the charge rate and the battery lifetime as well as for the removal of dendrites made possible by this technique. The least that can be said is that "it does not damage the battery".
IUI Charging
This is a recently developed charging profile used for fast charging standard flooded lead acid batteries from particular manufacturers. It is not suitable for all lead acid batteries. Initially the battery is charged at a constant (I) rate until the cell voltage reaches a preset value - normally a voltage near to that at which gassing occurs. This first part of the charging cycle is known as the bulk charge phase. When the preset voltage has been reached, the charger switches into the constant voltage (U) phase and the current drawn by the battery will gradually drop until it reaches another preset level. This second part of the cycle completes the normal charging of the battery at a slowly diminishing rate. Finally the charger switches again into the constant current mode (I) and the voltage continues to rise up to a new higher preset limit when the charger is switched off. This last phase is used to equalize the charge on the individual cells in the battery to maximize battery life.
Trickle Charge
Trickle charging is designed to compensate for the self discharge of the battery. Continuous charge. Long term constant current charging for standby use. The charge rate varies according to the frequency of discharge. Not suitable for some battery chemistries, e.g. NiMH and Lithium, which are susceptible to damage from overcharging. In some applications the charger is designed to switch to trickle charging when the battery is fully charged.
Float Charge
The battery and the load are permanently connected in parallel across the DC charging source and held at a constant voltage below the battery's upper voltage limit. Used for emergency power back up systems. Mainly used with lead acid batteries.
Random Charging
All of the above applications involve controlled charge of the battery, however there are many applications where the energy to charge the battery is only available, or is delivered, in some random, uncontrolled way. This applies to automotive applications where the energy depends on the engine speed which is continuously changing. The problem is more acute in EV and HEV applications which use regenerative braking since this generates large power spikes during braking which the battery must absorb. More benign applications are in solar panel installations which can only be charged when the sun is shining. These all require special techniques to limit the charging current or voltage to levels which the battery can tolerate.
|